Craft Campany / Sewing Pins with Flower in Gold, Silver and Bronze
Story to show Japanese craftsmanship through the things, the place and the people related to Cohana’s products. Our fourth story is Sewing Pins with Flower in Gold, Silver and Bronze by Craft Campany.
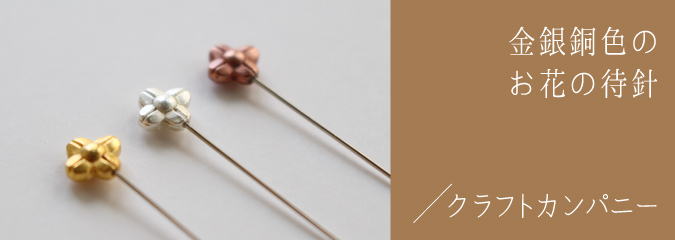
Osaka has a large clothing wholesaler district called “Semba Center Building” in the center of the city.
Although the area has a strong image of takoyaki (octopus dumplings) and comedy, it is actually a very convenient town where you can find your favorite materials and parts within a short walk of the Semba Center Building and other clothing-related workshops and companies.
The Craft Company is located in Ikuno-ku, Osaka, where many factories for buttons, accessories, and other accessories are located. The Craft Company is located in a quiet residential area.
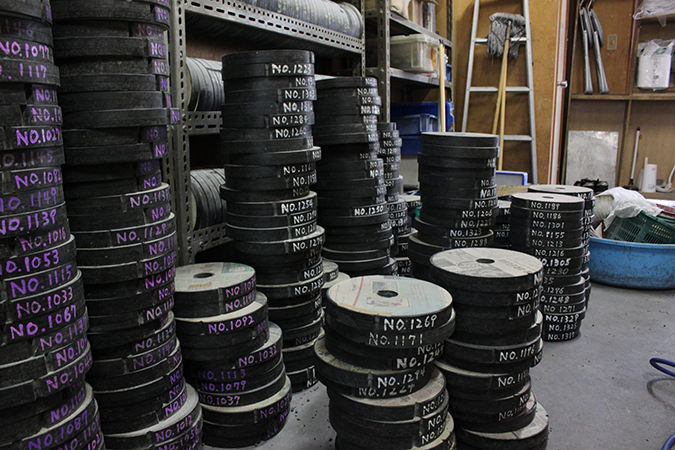
▲A lot of rubber discs in their garage.
Craft Company,founded in 1963,is a metal manufacturing company that mainly produces accessory parts. The company’s specialty is the “rubber casting method,” in which a rubber mold is made from a rough shape carved out of wax.
We wanted to put a delicate cute little flower for the top of our sewing pins. Craft Company, which has captured the hearts of many women through their works, will surely fulfill our ideal.
With the great conviction, we asked Craft Company to produce lovely flower-shaped pins heads.
Let’s see how they are made. Starting from Wax Processing.
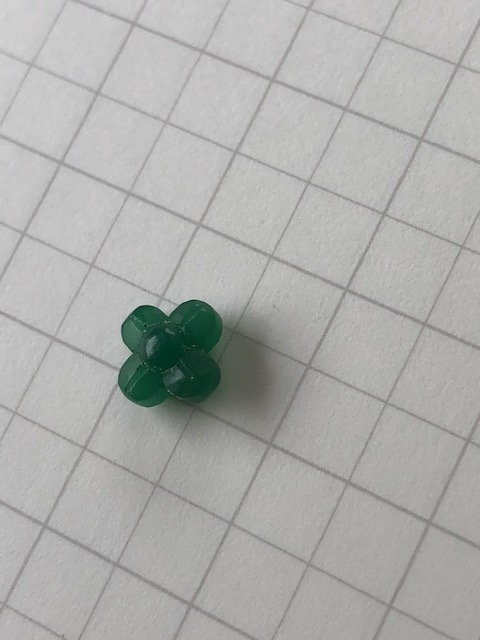
▲The tiny little green wax was carved into a tiny little flower by the artisan. On the 5mm grid paper you can tell how tiny it is.
First, based on the blueprint, the artisan cut the wax one by one.
The petal was delicately reproduced on a small wax flowerwith a diameter of 7mm,which we had requested.
Looking at the piece of wax, it’s hard to imagine how they would turn out as a metal part.
Experienced artisan carves wax looking for the best results as a metal part. The craftsmen think about these things every day as they work.
By pouring silver into the gaps created, a hard metal mold is completed.
By pouring silver into the gaps created, a hard metal prototype is completed.
From here, the process of replication using rubber begins.
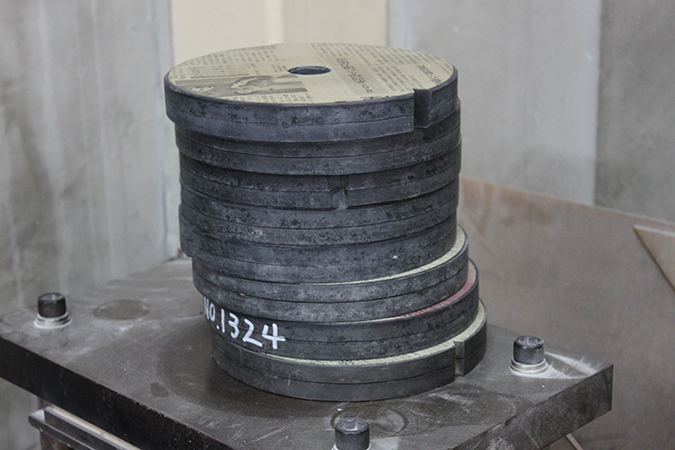
▲For the rubber casting method, they use rubber discs, a set of two pieces, top and bottom. The inside of the rubber discs is delicate and soft to mold delicate design. If you press it with finder, it can memolize your fingerprint.
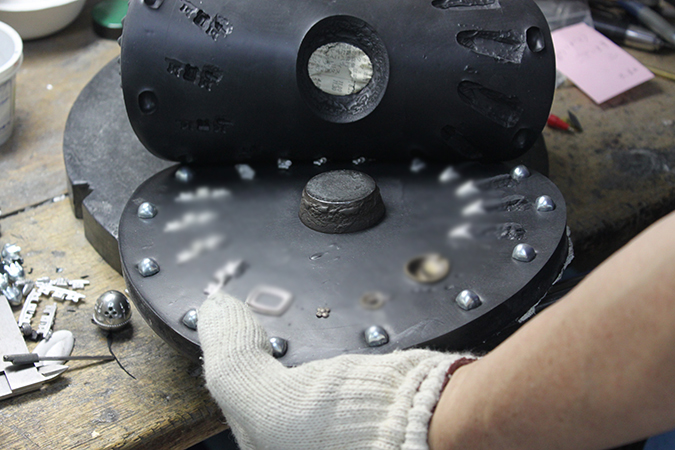
▲Place a silver metal mold in the rubber and press.If you repeat this process, you can make many identical molds.
Unlike the first wax mold, the mold made of hard silver will not break even if this process is repeated several times.
Once the patterns of the mold are made on the disc, a grooves are dug for the alloy to flow through, which is called a “path”.
Since the alloy is poured in using a centrifuge, this is a manual process using a cutter, keeping in mind the direction of rotation.
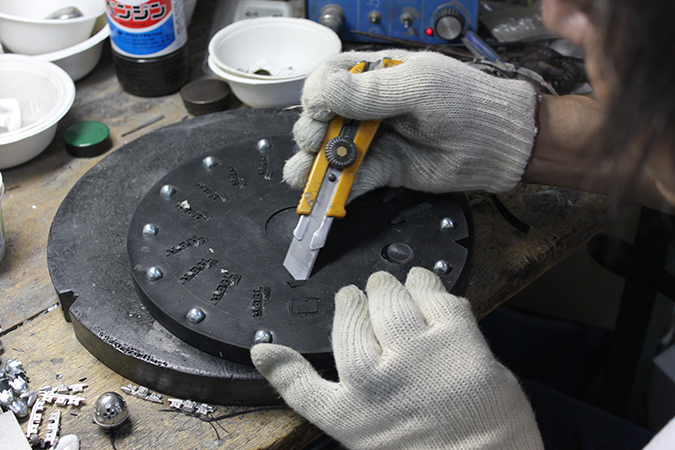
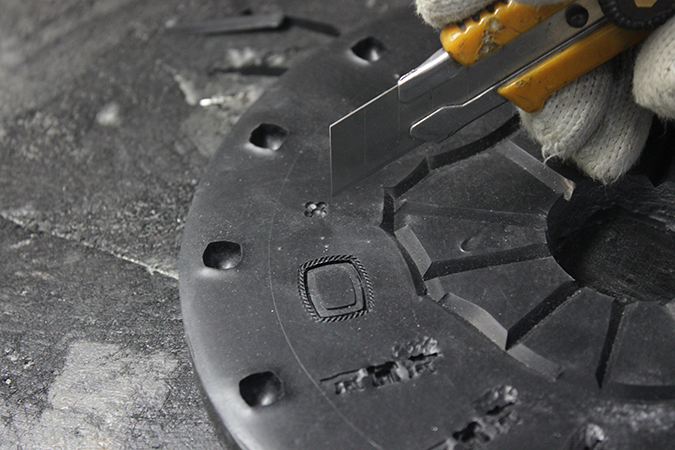
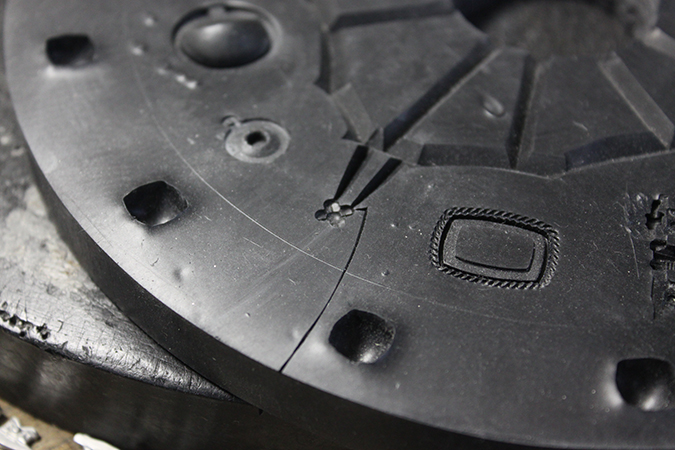
▲Also create a narrow path for the overflowing alloy to escape outward.
Finally, the alloy is poured in.
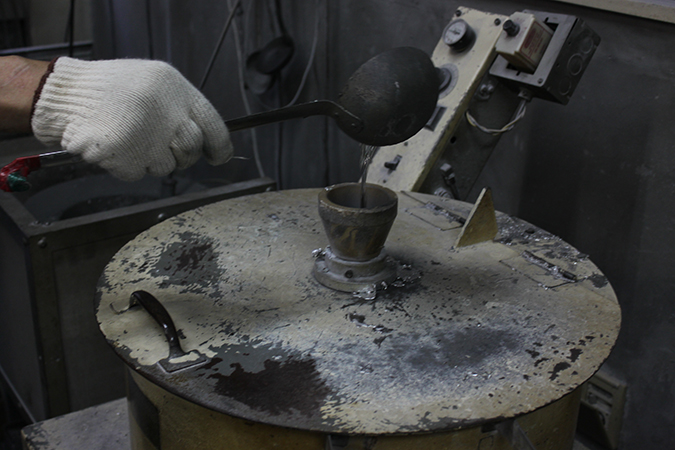
▲The mold is placed in a centrifuge, and with the machine spinning at high speed, the liquid tin alloy is poured through the hole in the middle.

▲Spider web shape casted tin alloy appears in between the discs.
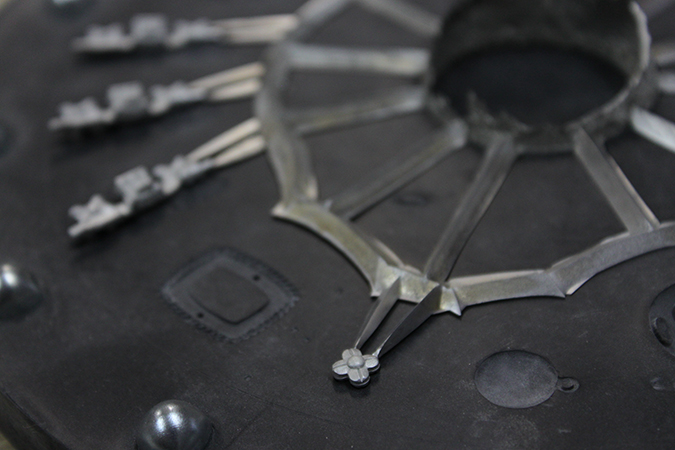
▲The tin alloy ran along the “path” that were craved and safely made its way to the parts of the flower.
The amount of tin that is poured in and the way it is carved is a very important skill for the craftsman. If the amount of tin alloy is too little, it will not take shape. If the amount of tin alloy is too much, it will be difficult to remove burrs (excess metal that has been attached to the surrounding area). It may look simple, but it is a work that requires fine adjustments.
Finally, the part is finished by deburring, barrel polishing, and plating.

▲One by one, the staffs deburr the pieces.
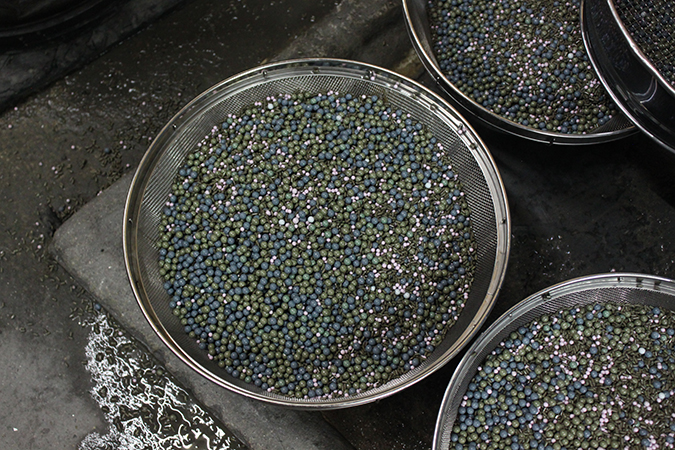
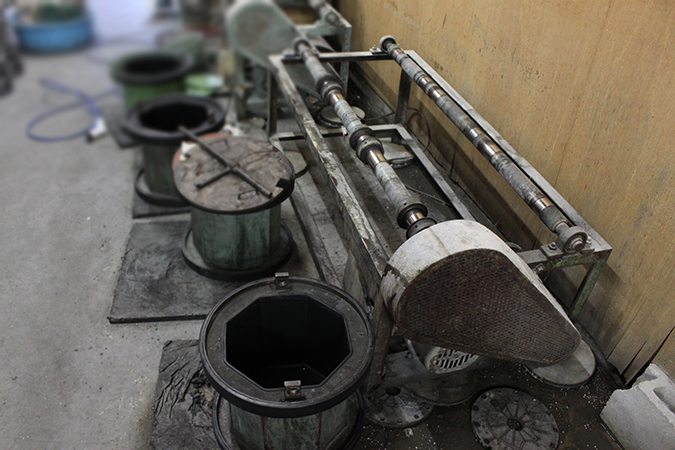
▲”Barrel Polishing” Parts are placed in a barrel containing beads of various shapes, and the surface of the parts is polished by rotating the barrel.
Even looking at these processes, we could see that there was a lot of manual labor involved in each process.
Next we interviewed the artesian at the office.
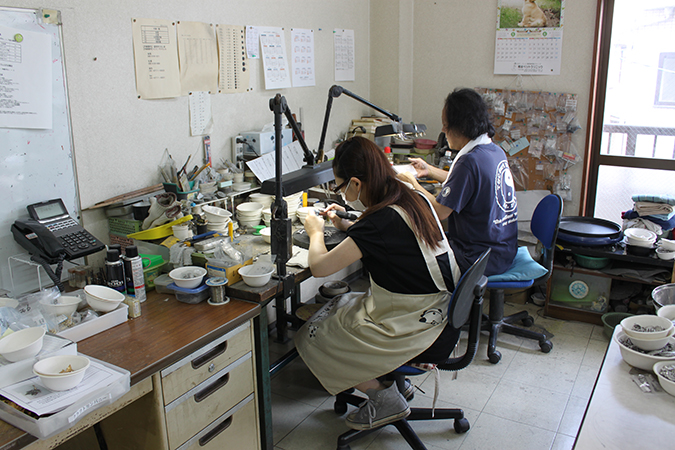
ーIs the “rubber casting process” an old technology?
I heard that the technology came from the U.S. after the World War II. We mainly produce accessories now, but at the time when the technology was introduced, button production was the mainstream technology. I guess button making was a bit more simple and rough compared to accessories, which require fine lines and small details.
Once the technology was introduced, rubber-cast buttons began to replace the brass cast buttons that had been the mainstream, and the number of companies adopting this method increased rapidly.
ーI see that from the creator’s point of view, introduction and production was both easier.Were there any advantages or product advantages for the customers as well?
The rubber casting process uses a tin alloy or antimony, which is lighter than brass, and applies plating of various colors and textures on it.
I think the appeal of this method is that it is lighter than brass buttons and allows for more delicate expressions. When I first came to Japan, there was a particular demand for buttons for knit cardigans. When the buttons are heavy, the fabric stretches and you don’t like that, do you? The rubber casting method has solved this problem.
Buttons made of rubber casting were often used for citizen’s clothes after the war. Perhaps there was an invisible connection between the light and colorful rubber-cast buttons and the hearts of the Japanese people, who were moving toward economic growth after overcoming a dark period.
ーI see. So the rubber casting method is still in common use today?
Actually, the use of the rubber casting method has decreased considerably compared to the postwar periods. The main products made by the rubber casting method were buttons and accessories, and the choice of which of these two as the main focus of the business has made the difference.
ーWhat do you mean?
Accessory making requires higher level of skills, such as watermark patterns, very small parts, and delicate orders. It’s a tough job, but each time we meet the various challenges demanded by our customers, the skills of our craftsmen improve. As a result, more accessory parts manufacturing companies have been able to develop excellent craftsmen and this is why they are survived in the business.
ーThe accumulation of steady work led directly to the skills of the craftsmen. It was a very interesting story. Thank you very much.
In the end, they showed us a delicate part using old molds inherited from their predecessors.
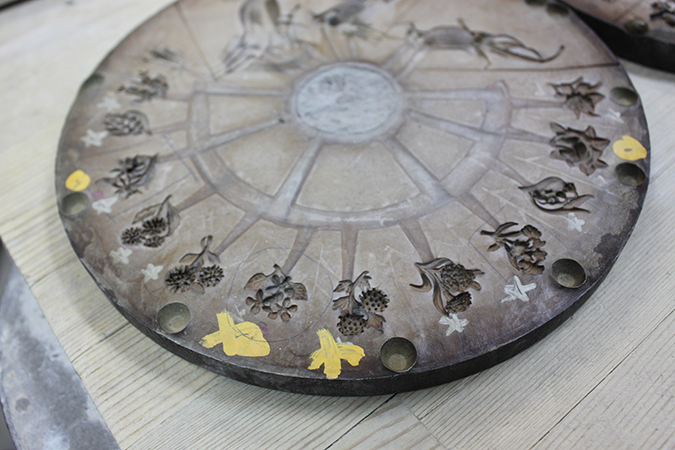

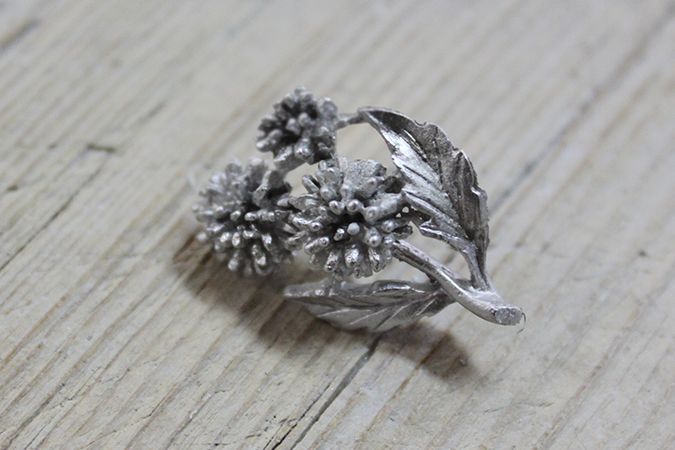
From the aged rubber, parts for accessories in the shape of small flowers and birds appeared. I couldn’t help but sigh at the cuteness and delicacy of them.
I’m sure the women who picked this up at the time would have felt the same way.
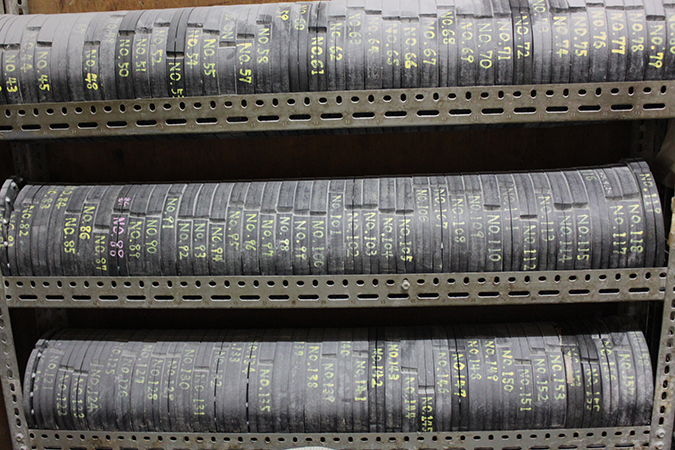
The many rubbers I saw in the garage were an accumulation of the history of the Craft Company and the skills of its craftsmen.
The gold-, silver-, and copper-colored flower waiting needles are small products, but they are filled with the “wisdom and history” that the hands of craftspeople have connected.
I left the factory impressed by the power of the town factory that had accumulated experience and flexibly to the changing times.
Craft Company
Osaka’s Ikuno Ward is near a district of clothing wholesalers, and contains many small neighborhood workshops producing buttons and accessories. Craft Company has used rubber casting since its founding in 1963.